E-SEED: Self-burying Seed Carrier
615 (2023 Feb 15)
Agriculture and reforestation: Bioinspired seed carrier improves on nature.
By Danli Luo, Aditi Maheshwari, Andreea Danielescu, Jiaqi Li, Yue Yang, Ye Tao, Lingyun Sun, Dinesh K. Patel, Guanyun Wang*, Shu Yang*, Teng Zhang*, Lining Yao*.
DOI | Nature cover story | Nature News | Nature Video
Freely access the paper online | Media Package Download
News: BBC | Science Friday | Nature News | NewScientist | Reuters | Plantae| CMU News | Penn Today | Nature Biotechnology | Tulsa World | Seed World | Futurity
Collaborative Institutes:
Morphing Matter Lab, Human-Computer Interaction Institute, Carnegie Mellon University (Leading)
Syracuse University
University of Pennsylvania
Accenture Labs
Zhejiang University
2023 Jun 1 - 25
Aerial seeding is a crucial way to cover large and otherwise inaccessible areas, and can facilitate post-fire reforestation or wildland restoration. However, when a seed lies on the surface, it can be damaged by weather conditions or eaten by wildlife, resulting in low germination rates.
A new biodegradable seed carrier design inspired by the self-drilling behaviour of Erodium seeds is described in a paper in Nature. The seed carrier has a higher implantation success rate than that of Erodium seeds. This technology may improve the effectiveness of aerial seeding to address agricultural and environmental stresses in degraded regions.
The team designed a wood-based biodegradable seed carrier that mimics seeds of Erodium, a genus of plants with seeds that unwind coiled tails to act as a drill to plant into the ground. The seed carrier has three coiled tails attached that unwind when moistened and can carry seeds as large as those of whitebark pine trees, which are about 11 mm long and weigh about 72 mg. Increasing the number of unwinding tails ensures the drill bit is better angled to the surface for burrowing. The seed carriers had an 80% success rate of getting seeds into the ground on flat land, reducing the risk of them blowing away or being eaten by animals. Under the same terrain conditions, the natural Erodium seed’s success rate was 0%. The carriers could also be used to deploy fertilizers or other materials (such as sensors) that could be beneficial for agricultural and conservation applications, the authors conclude.
Multi-functionality
The geometric-based designs allow us to tailor the self-burial seed carriers for different terrain conditions and payloads.
Design Variations
Different engineered seed carrier designs with different size, coil and tail variations.
Seed and Sensors
The self-burying seed carrier can be used to deliver functional devices, such as sensors, fertilizers and different plant seeds.
Self-burying
We conducted five outdoor drilling experiments with 136 three-tailed seed carriers in two geographical locations over two springs.
This self-burying seed carrier system is expected to improve the effectiveness of aerial seeding to relieve agricultural and environmental stresses, and has potential applications in energy harvesting, soft robotics and sustainable buildings.
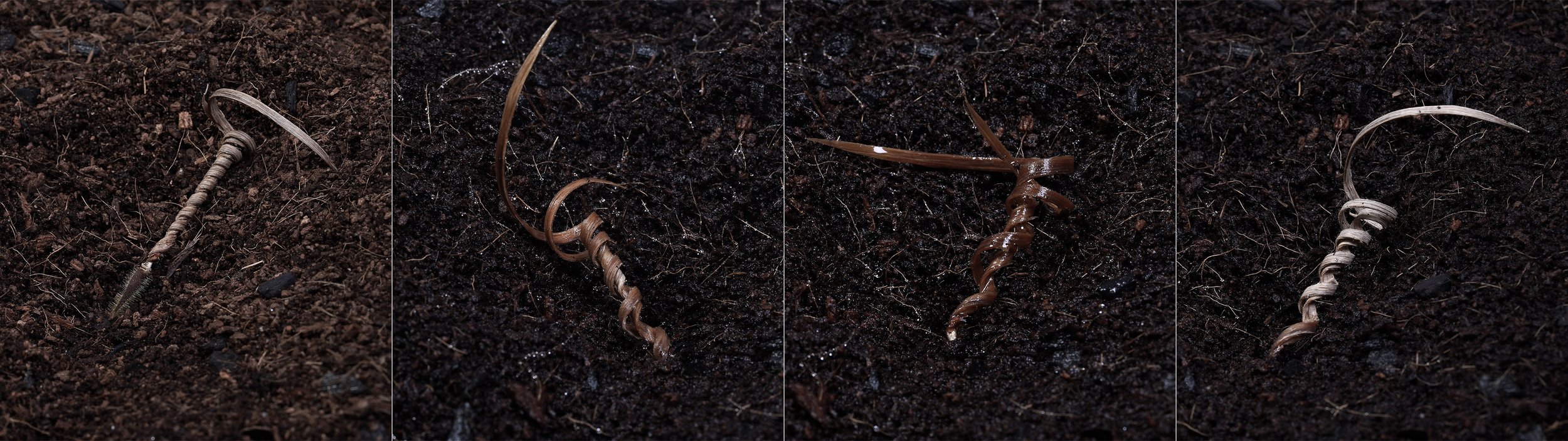
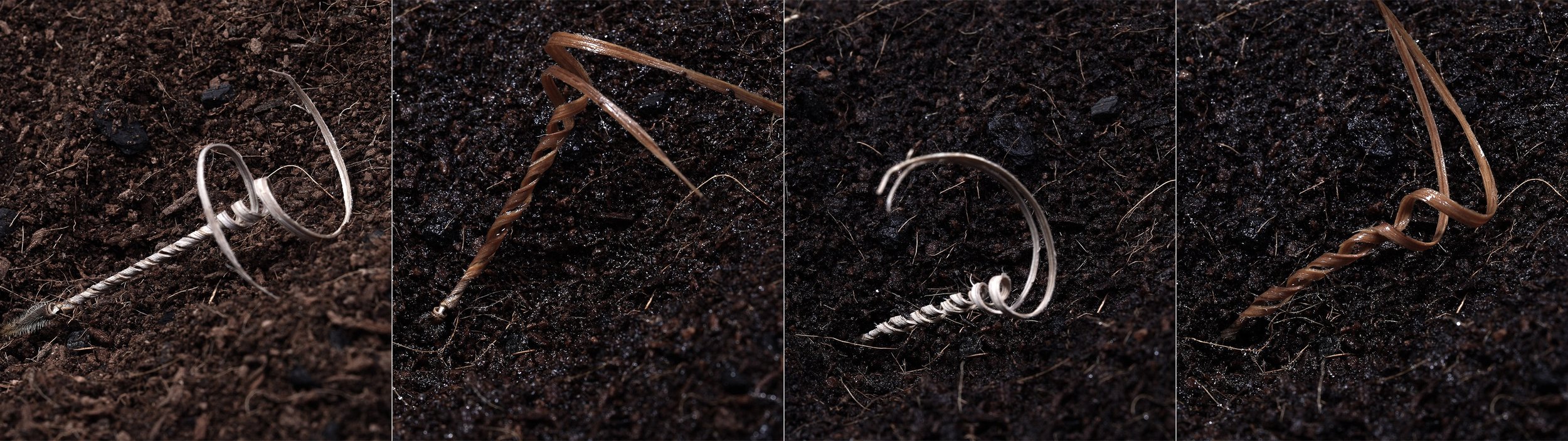
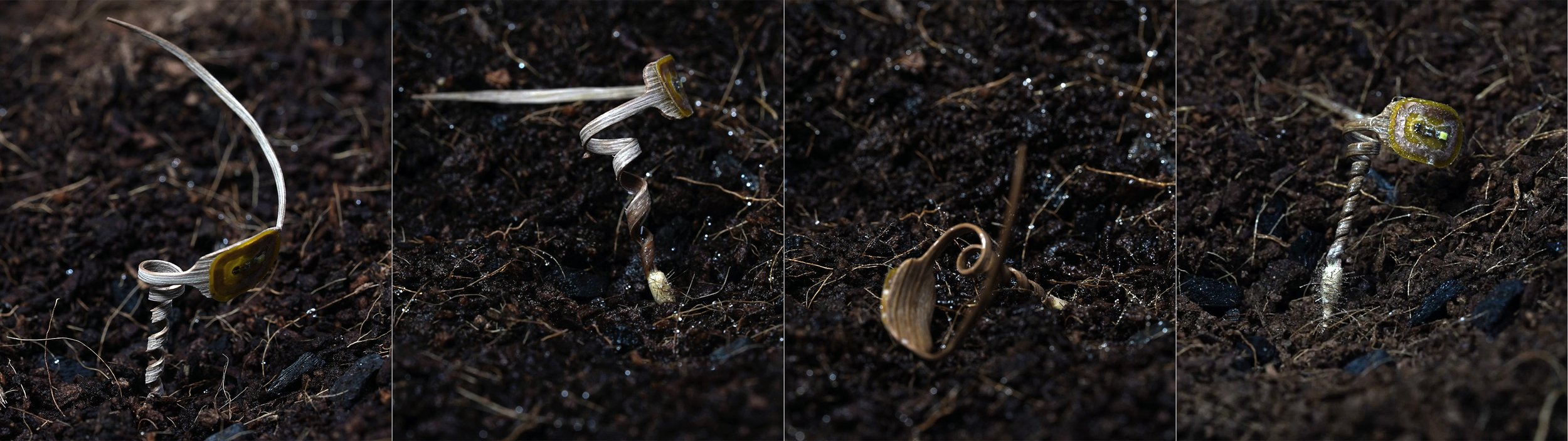
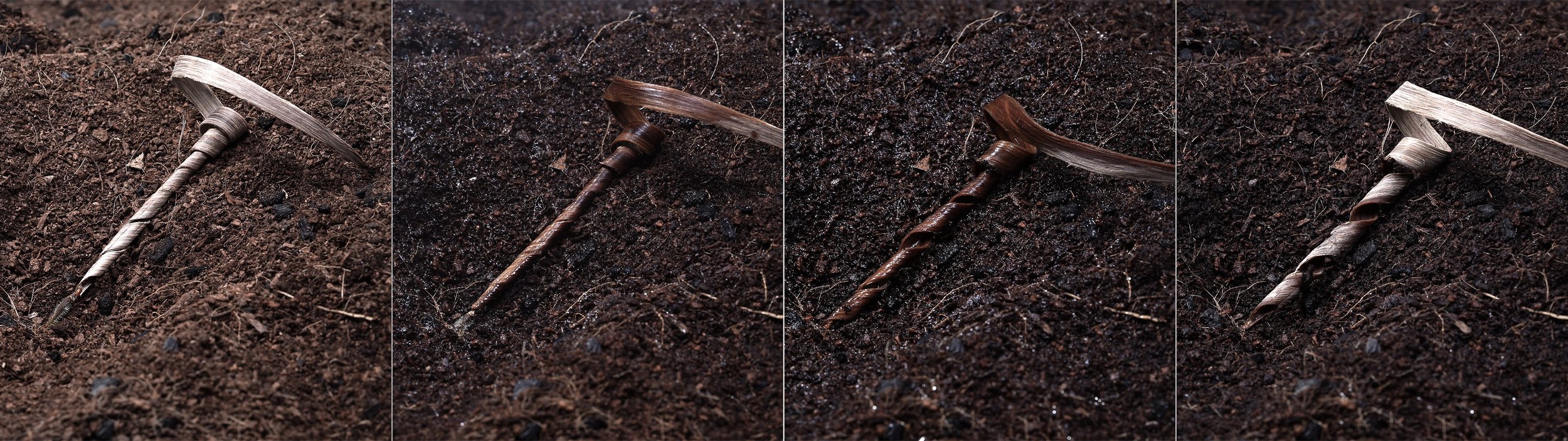
Aerial Delivery
We customized a delivery mechanism for the drone-delivery test outdoor.
Germination
We embedded two cherry belle radish seeds and 1 mg of mycorrhizal fungi within one tip. After 9 days, the seeds germinated and the fungi was visible under a light microscope.
Field Test
In the years 2021 and 2022, the team conducted five outdoor drilling experiments with 136 three-tailed seed carriers in two geographical locations over two springs in both the US and China. We learned that the performance of our system varies a lot depending on the environmental conditions, such as precipitation rate and temperature, as well as the soil conditions. Design customizations can be made to tailor different design optimizations to different physical constraints.
Model and Simulation
Data from experiments and numerical simulation have been used to elucidate the curvature transformation and actuation mechanisms to guide the design and optimization of the seed carriers.
The seed carriers have an 80% drilling success rate on flat land after two triggering cycles, due to the beneficial resting angle (25°–30°) of its tail anchoring.
Manufacturing
It is a five-step process involving both chemical washing and mechanical molding.
The manufacturing steps create wood-based hygromorphic actuators with a large initial curvature.
Listen to the team talking about their process of designing and manufacturing E-seed:
Microstructure
To drill into natural terrain by harvesting ambient moisture fluctuations, the carrier should be hygromorphic with a large bending curvature and tightly coiled when dry. Natural wood has well-studied hygromorphic properties and is an abundant and environmentally friendly structural material.
A set of representative scanning electron micrographs of the wood strip after moulding and drying: the deformed cells towards the inner side tend to have larger MFAs than the cells towards the outer side with relatively smooth cell walls.
Acknowledgment
Chengyuan Wei, Morphing Program Co. Processing suggestions.
Eran Sharon, Hebrew University of Jerusalem. Mechanism discussion.
Liangbing Hu, University of Maryland. Scientific insight.
Jianzh Gu, Carnegie Mellon University. Computational design.
Jack Forman, MIT Media Lab. Mechanism discussion.
Junyun Zhu, US Department of Agriculture Forest Products Laboratory. Discussions and characterization through X-ray diffraction.
Nayomi Plaza, US Department of Agriculture Forest Products Laboratory. Discussions and characterization through X-ray diffraction.
Special thanks to Prof. Hiroshi Ishii and Neri Oxman, who served on Prof. Lining Yao’s PhD thesis committee in 2016-2017, when the self-burying Erodium seed was first discussed in her thesis proposal as future work.
Funding
US National Science Foundation IIS-CAREER-1847149 (Lining Yao)
US National Science Foundation CMMI-2020476 (Teng Zhang)
US National Science Foundation The Future Eco Manufacturing Research Grant, no. CMMI 2037097 (Shu Yang)
The Triton Shared Computing Cluster at the San Diego Supercomputer Center and the Expanse cluster (TG-MSS170004, Teng Zhang) in the Extreme Science and Engineering Discovery Environment.
Materials Characterization Facility at Carnegie Mellon University (MCF-677785, Lining Yao)
The National Natural Science Foundation of China (62002321, Guangyun Wang)
A gift to Carnegie Mellon University (Lining Yao) from Accenture Labs.
Credit
Project Execution:
Project Lead and Supervising: Lining Yao (liningy@andrew.cmu.edu),
Experimental Lead: Danli Luo (luo.denier@gmail.com )
Experimental Lead and Supervising: Guanyun Wang (guanyun@zju.edu.cn)
Modeling and Supervising: Teng Zhang (tzhang48@syr.edu)
Supervising: Shu Yang (shuyang@seas.upenn.edu)
User Study: Andreea Danielescu (andreea.danielescu@accenture.com )
User Study: Aditi Maheshwari (aditi.maheshwari@accenture.com)
Nature Paper Contributions:
L.Y. and D.L. conceived the initial concept. A.M. and A.D. conceived two application contexts. L.Y., T.Z., S.Y. and G.W. supervised the project. L.Y., D.L., T.Z. and S.Y. wrote the manuscript. D.L., L.Y. and G.W. carried out fabrication and peak force measurements. D.L., L.Y., G.W., J.L., Y.Y., Y.T. and L.S. carried out drilling and germination tests. D.L., L.Y. and Y.Y. carried out bending angle and coil pitch measurements. D.L., L.Y. and D.K.P. carried out scanning electron microscopy and micrograph analysis. D.K.P. and L.Y. conducted tensile tests. T.Z. and L.Y. carried out curvature analysis. T.Z. carried out mechanical modelling and simulation. S.Y., T.Z. and L.Y. provided scientific and experimental advice. L.Y. and D.L. created the videos.
Collaborative Institutes
Morphing Matter Lab, Human-Computer Interaction Institute, Carnegie Mellon University (Leading)
Accenture Labs
Computer Science and Technology, Zhejiang University.
School of Artistic Design and Creation, Zhejiang University City College.
Materials Science and Engineering, University of Pennsylvania.
Department of Mechanical and Aerospace Engineering, Syracuse University
BioInspired Syracuse, Syracuse University
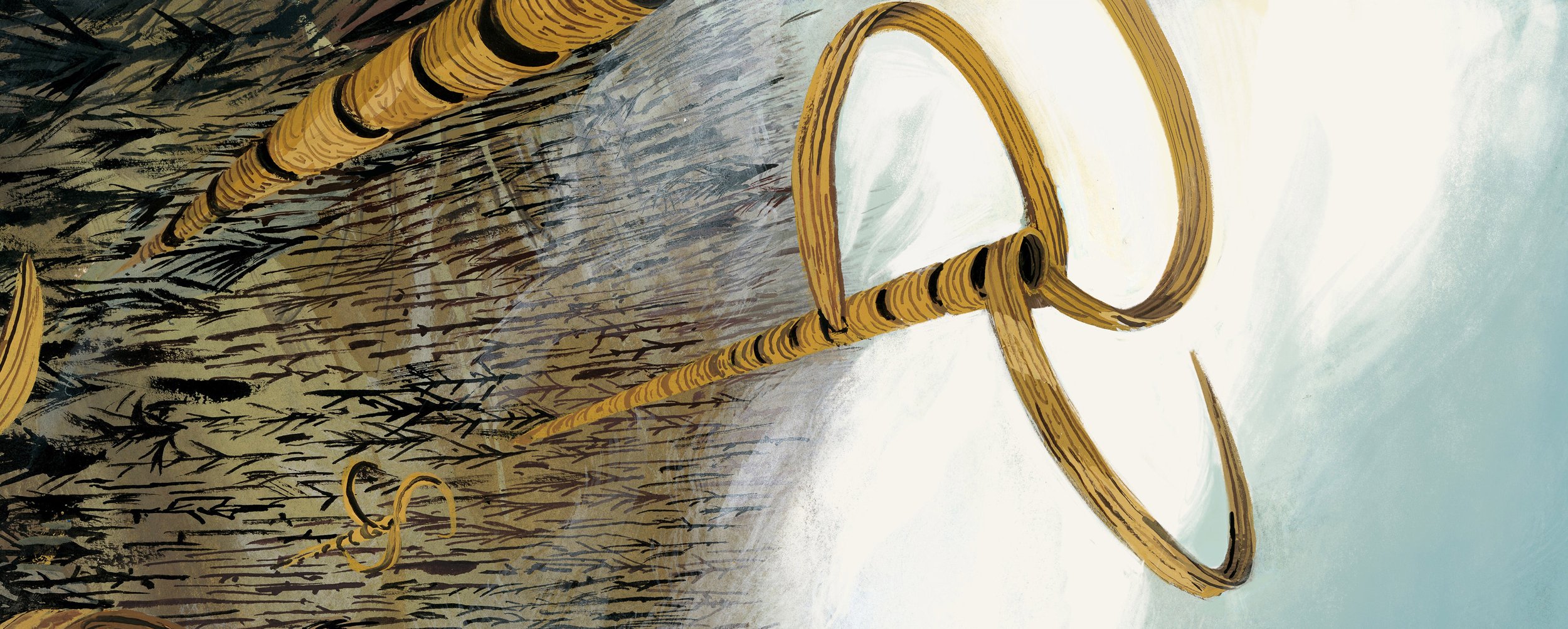
Contact
Lining Yao
liningy@andrew.cmu.edu
Illustration by: Tara Anand